Graphite bipolar plate for fuel cell
Graphite bipolar plate for fuel cell – fuel cell coating – Cheersonic
Graphite is the earliest bipolar plate material developed. Compared with metal and alloy bipolar plates, graphite bipolar plates have the advantages of low density, good corrosion resistance, and good affinity with carbon fiber diffusion layers, which can meet the requirements of long-term stable operation of fuel cells. However, graphite has high porosity, low mechanical strength, and high brittleness. In order to prevent the working gas from penetrating the bipolar plate and meet the design of mechanical properties, the graphite bipolar plate is usually thicker, resulting in larger volume and mass of graphite materials. . In addition, due to poor processing performance and low yield of graphite materials, manufacturing costs increase.
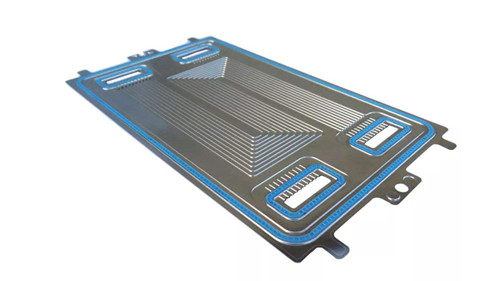
Pure graphite plates are generally prepared with carbon powder or graphite powder and pitch or graphitizable resin. The graphitization temperature is usually higher than 2500°C, and the graphitization process must be carried out in accordance with a strict heating program, and the preparation cycle is long, which leads to high prices of pure graphite plates. Graphite worms expanded with expandable graphite are directly pressed to produce flexible graphite plates of different densities. These flexible graphites have stable performance, good electrical conductivity, corrosion resistance, self-sealing effect and easy processing. They are good flow field plate materials.
Some scientists have proposed a method for preparing a whole piece of graphite board, the sealing edge part is non-porous or extremely small, but the working part has a large porosity, which leads to high energy consumption; the vacuum pressure method is impregnated with sodium silicate concentrated solution Graphite bipolar plates are then heated to convert them into SiO2. This method greatly reduces the porosity. In addition, scientists have also used graphite powder and carbonized thermosetting phenolic resin to mix injection molding to prepare bipolar plates. The strength of the bipolar plate prepared by this method meets the requirements of the fuel cell, but the resistivity is large, about 10 times larger than that of the pure graphite bipolar plate; the graphite flakes are superimposed, and the graphite and the supporting material plate are combined The bipolar plates are made together, and the current density and battery voltage of the bipolar plate materials are significantly improved; the method of coating a thin layer of metal on the graphite plate is used to avoid degradation of the resin in the material.
It can be seen that the graphite bipolar plate material has good corrosion resistance and electrical conductivity, which can meet the requirements of long-term operation of the bipolar plate, but the processing performance of the graphite material is poor, and the manufacturing cost is high. The mechanical properties and cost of the polar plate have been greatly improved, but the mechanical properties and cost requirements of the bipolar plate still cannot be met, which is still the biggest bottleneck restricting the widespread use of graphite bipolar plates.