Perovskite Solar Cells
Ultrasonic spraying is a promising way to expand the production of perovskite solar cells, and it can be prepared at any scale from laboratory to mass production. Unlike spin coating, however, it is difficult to describe the spray process through a set of machine-independent parameters. In this work, an in-situ measurement and modeling of wet film thickness and evaporation rate was proposed as an independent description of the machine for the ultrasonic spraying process, and applied to process optimization for the preparation of high-performance perovskite solar cells. Optimization of physical wet film parameters rather than machine settings can better understand the key factors that affect film quality and can transfer the process to another manufacturing environment. The morphology of the sprayed PbI2 film was analyzed under a series of coating conditions, and a close correlation was observed between the spraying parameters and the uniformity of the PbI2 film. Premature precipitation and sparse nucleation are the reasons for the unevenness of the film, and the optimal process parameters have been determined. Under ambient conditions and a relative humidity of 50%, the device prepared after the optimized process achieved 13% power conversion efficiency in a device with an area of 1 cm2, and the hysteresis was negligible. Related work was published in Journal of Materials Chemistry A (J. Mater. Chem. A. 2017, 5, 5709-5718) under the title of “Transferrable optimization of spray-coated PbI2 films for perovskite solar cell fabrication”.
- Photographs of sprayed PbI2 and its perovskite films under different temperature substrates and ink pump speeds under an optical microscope
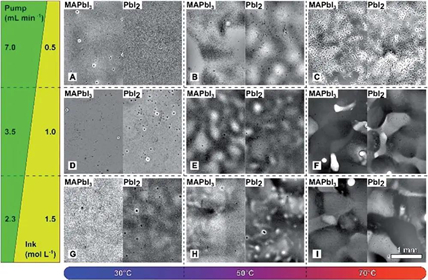
- i) Photographs of PbI2 and its perovskite film sprayed under different temperature substrates and ink pump rates under an optical microscope The ink pump speed and ink density change together to keep the amount of PbI2 per unit area constant. Row changes are temperature changes, and column changes are ink pump rate changes.
- Effect of liquid film thickness on microstructure of thin film
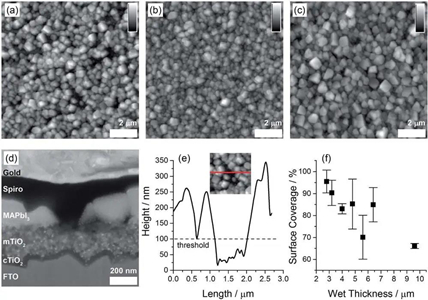
(a-c) AFM diagram of perovskite film: (a) 7 mL / min, (b) 3.5 mL / min, (c) 2.3 mL / min,
(d) Cross-sectional SEM image of a perovskite film with voids
(e) Highly schematic diagram of perovskite film with voids
(f) Relationship between surface coverage and wet film thickness of spraying process
- Relative characterization of wet films
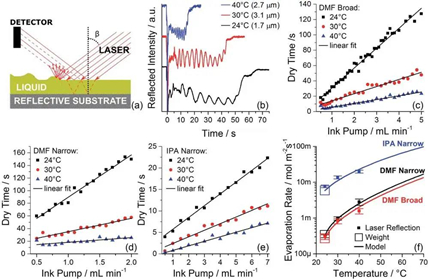
(a) Schematic diagram of measuring wet film thickness using laser
(b) Oscillation diagram of laser intensity after wet film evaporation
(c) Relationship between wide spraying, DMF wet film drying time and ink pump speed
(d) Relation between narrow spraying, DMF wet film drying time and ink pump speed
(e) Narrow spraying, IPA drying time
(f) Evaporation rate determined by drying time, measured disturbance value, direct mass change measurement value and model
- COMSOL simulates the surface evaporation rate of laminar airflow
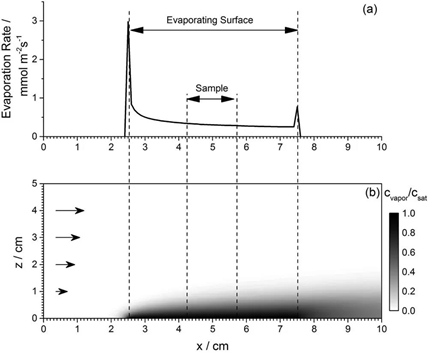
(a) Relationship between evaporation rate and location
(b) Vapor concentration above the sample
- Device efficiency
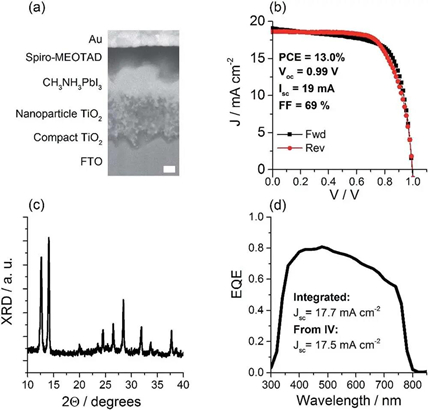
(a) Cross-section SEM image and structure diagram of perovskite device
(b) The forward and reverse sweep J-V curve of the optimal device
(c) XRD pattern of the optimal perovskite film
(d) IPCE curve of the optimal device
In this work, by optimizing the parameters, the PbI2 thin film with the best uniformity can be ultrasonically sprayed, and its thickness is suitable for preparing high-performance perovskite solar cells. We observe a strong correlation between wet film thickness, evaporation rate, and dry film uniformity, and determine wet film thickness and evaporation rate as key parameters of dry film quality. To facilitate the transfer of recipes from specific equipment in the laboratory to the production environment, this article shows a simple method to measure wet film thickness and evaporation rate in the field. In addition, it is demonstrated that the measurement of the evaporation rate of a single wet film can be used to determine the surface mass transfer coefficient of the process chamber. Knowledge of the surface mass transfer coefficient allows us to calculate the evaporation rate of the ink based on any solvent. Demonstrating the modeling of local evaporation rates, which allows necessary adjustments to process parameters when changing the geometry of the sample. Using the best process conditions, we have prepared perovskite solar cells, whose device performance is comparable to the best performance achieved by sprayed devices with an effective area of 1 cm2.
Original link: https://pubs.rsc.org/en/content/articlelanding/2017/TA/C6TA09922J#!divAbstract