Ultrasonic Spraying Fuel Cell GDL
Ultrasonic Spraying Fuel Cell GDL – Coating Gas Diffusion Layer
Maximizing the use of GDL in the Fuel Cell by ultrasonic spray application
The Gas Diffusion Layer (GDL) plays several critical roles in a typical fuel cell application and is often integrated as part of the Membrane Electrode Assembly (MEA). Typical applications that use GDLs consist of Polymer Electrolyte Fuel Cells (PEMFC) and Direct Methanol Fuel Cells (DMFC). When a GDL is coated with a catalyst it is than referred to as a Gas Diffusion Electrode (GDE), which are sometimes sold or installed separately from the Membrane or MEA. Acting as an electrode is the easy part of the GDL/GDE, though.
The GDL is a porous structure made by weaving carbon fibers into a carbon cloth (e.g. GDL-CT and ELAT) or by pressing carbon fibers together into a carbon paper (e.g. Sigracet, Freudenberg, and Toray).Many of the standard GDLs that are produced today come with a Micro Porous layer (MPL) and hydrophobic treatment (PTFE). The MPL and PTFE help with the contact to the membrane and with water management. The MPL typically provides a smooth layer with plenty of surface area for catalyst and good contact with the membrane.
The MPL often uses PTFE as a binder that increases hydrophobicity, which helps keep the water within the membrane from escaping – drying out the membrane and causing higher resistance (lower performance). There is often an additional PTFE coating on the MPL surface to further augment this.
GDL essentially acts as an electrode that facilitates diffusion of reactants across the catalyst layered membrane. The surface area and porosity of the GDL is what allows for the reactants in the channels of the bipolar plate to diffuse along the active area (catalyst area) of the membrane.With the increased surface area that the GDL provides, transportation of electricity from each individual catalyst site in the Membrane Electrode Assembly (MEA) to the current collectors increases.
The GDL is also the component that handles the fuel cell moisture control. It does this by consistently helping to remove the by-produced water outside of the catalyst layer and prevent flooding chambers. The GDL also helps keep some water on the catalyst layer surface to improve conductivity throughout the membrane. It is also important to note that the GDL allows for heat transfer during cell operation as well.
Important consideration must also be made in regards to the mechanical properties of the GDL material since it is often compressed or partially compressed when the fuel cell stack is assembled.This compression can act as a bit of a “spring” to help accommodate for some of the thermal expansion larger fuel cell stacks can see in operation.
Cheersonic has committed to the research and development of various ultrasonic equipment for more than ten years. We will design a suitable plan according to the different needs of customers. CENG-S, CENG-M and CENG-L developed by our company is basic , programmable micro material spray coating system. Various types of catalysts suspensions including the carbon black ink , PTFE binder, ceramic slurry, platinum and other precious metal can be sprayed by using these equipment. Cheersonic ultrasonic dispersion syringe pump is 25 ml glass syringe standard, by controlling module delivers electrical impulses to generate ultrasonic vibrations inside of syringe body, and duration and intensity of ultrasonic vibrations is user controlled to completely disperse and hold particles evenly suspended in solution for up to several hours.
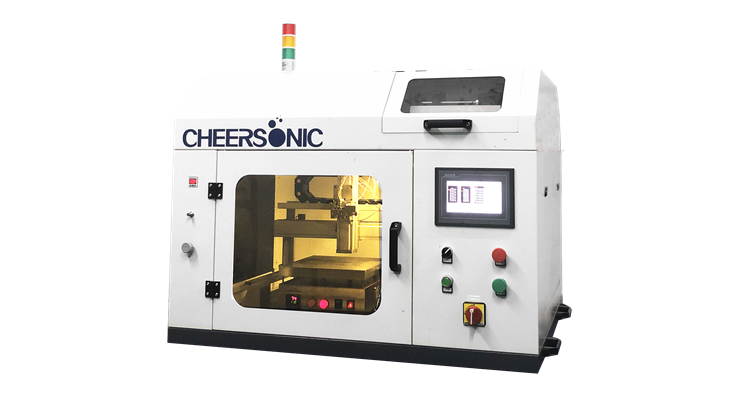